What is Porosity in Welding: Best Practices for Preventing Permeable Welds
Wiki Article
Porosity in Welding: Identifying Common Issues and Implementing Finest Practices for Avoidance
Porosity in welding is a pervasive issue that frequently goes undetected up until it triggers significant troubles with the stability of welds. In this conversation, we will certainly explore the vital elements adding to porosity formation, examine its harmful impacts on weld efficiency, and discuss the ideal practices that can be adopted to minimize porosity incident in welding procedures.Usual Sources Of Porosity

Making use of filthy or damp filler materials can present contaminations into the weld, contributing to porosity concerns. To mitigate these usual causes of porosity, thorough cleaning of base steels, correct protecting gas selection, and adherence to optimum welding specifications are necessary techniques in attaining top quality, porosity-free welds.
Effect of Porosity on Weld Quality

The presence of porosity in welding can considerably endanger the architectural integrity and mechanical properties of welded joints. Porosity develops gaps within the weld metal, weakening its total toughness and load-bearing capability.
Among the key repercussions of porosity is a reduction in the weld's ductility and toughness. Welds with high porosity degrees tend to show lower impact toughness and reduced capability to deform plastically prior to fracturing. This can be particularly concerning in applications where the bonded parts go through dynamic or cyclic loading conditions. Furthermore, porosity can hinder the weld's ability to successfully transfer forces, bring about early weld failure and possible safety and security hazards in important frameworks.
Finest Practices for Porosity Prevention
To enhance the structural stability and high quality of bonded joints, what particular actions can be applied to lessen the occurrence of porosity during the welding procedure? Porosity avoidance in welding is important to guarantee the honesty and strength of the final weld. One efficient practice is proper cleaning of the base steel, getting rid of any you can try these out kind of contaminants such as corrosion, oil, paint, or moisture that could result in gas entrapment. Guaranteeing that the welding tools remains in excellent problem, with tidy consumables and proper gas flow prices, can likewise dramatically lower porosity. In addition, preserving a stable official website arc and managing the welding parameters, such as voltage, present, and travel speed, helps create a constant weld swimming pool that minimizes the danger of gas entrapment. Utilizing the proper welding strategy for the certain material being bonded, such as changing the welding angle and gun placement, can even more prevent porosity. Routine evaluation of welds and prompt remediation of any type of issues determined during the welding process are crucial techniques to protect against porosity and produce high-quality welds.Importance of Appropriate Welding Methods
Carrying out appropriate welding techniques is paramount in making sure the structural integrity and quality of bonded joints, developing upon the structure of effective porosity avoidance actions. Too much heat can lead to increased porosity due to the entrapment of gases in the weld pool. Additionally, using the ideal welding parameters, such as voltage, existing, and travel speed, is critical for attaining audio review welds with marginal porosity.Moreover, the choice of welding procedure, whether it be MIG, TIG, or stick welding, must straighten with the certain requirements of the job to make sure ideal outcomes. Proper cleansing and preparation of the base metal, in addition to selecting the ideal filler product, are also vital parts of skillful welding techniques. By sticking to these best techniques, welders can lessen the danger of porosity formation and produce premium, structurally audio welds.
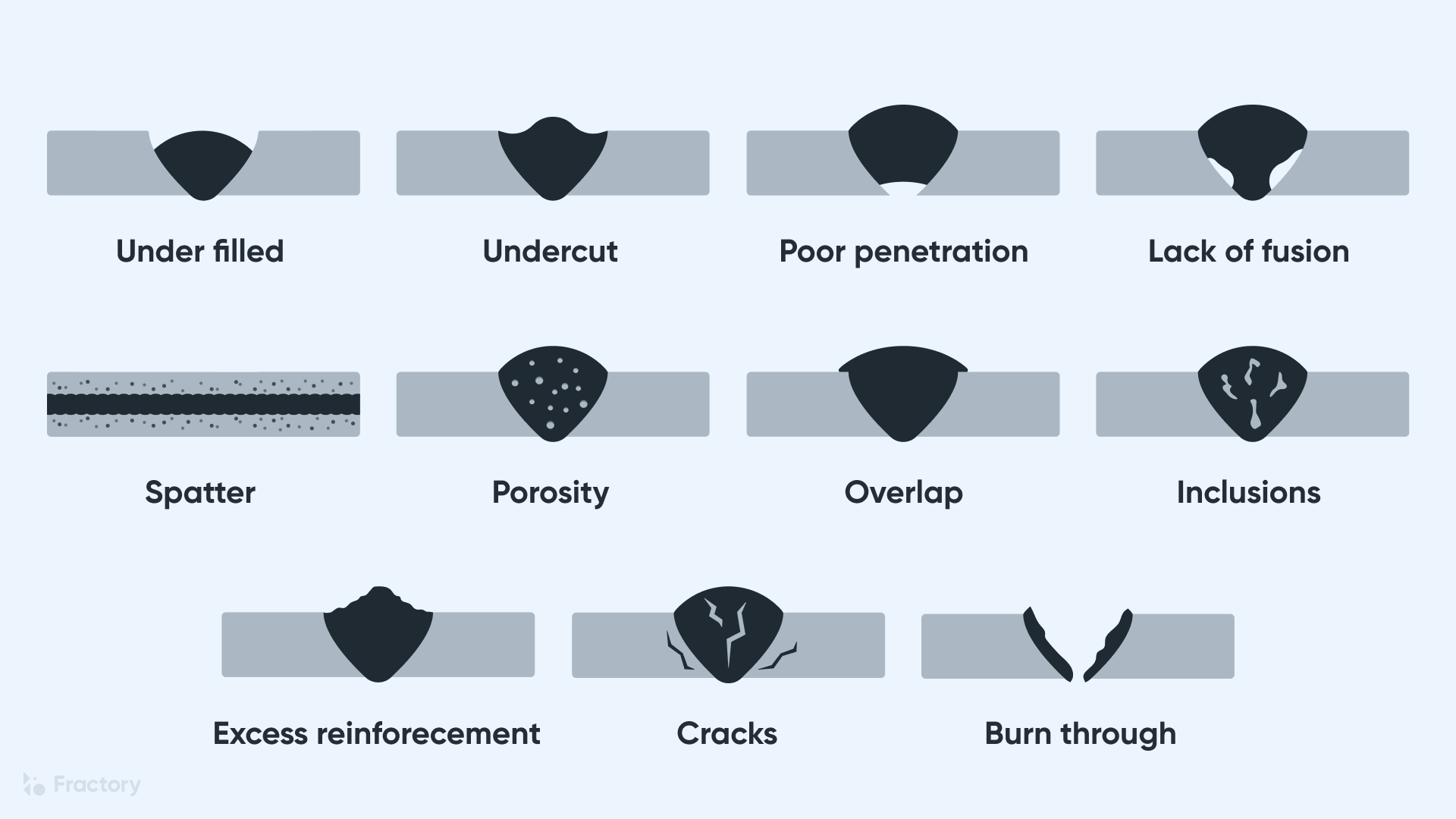
Examining and High Quality Control Steps
Quality assurance measures play a critical role in confirming the stability and integrity of bonded joints. Testing treatments are vital to detect and stop porosity in welding, making certain the strength and longevity of the end product. Non-destructive screening approaches such as ultrasonic testing, radiographic testing, and visual inspection are frequently used to determine potential issues like porosity. These strategies enable the assessment of weld high quality without compromising the honesty of the joint. What is Porosity.Post-weld inspections, on the other hand, examine the final weld for any type of flaws, consisting of porosity, and verify that it fulfills specified standards. Applying an extensive high quality control plan that includes thorough screening treatments and assessments is vital to decreasing porosity problems and making certain the overall top quality of welded joints.
Verdict
In conclusion, porosity in welding can be an usual concern that impacts the high quality of welds. By identifying the usual causes of porosity and applying best methods for prevention, such as correct welding methods and screening actions, welders can make sure excellent quality and trusted welds. It is important to focus on prevention methods to lessen the event of porosity and maintain the integrity of bonded frameworks.Report this wiki page